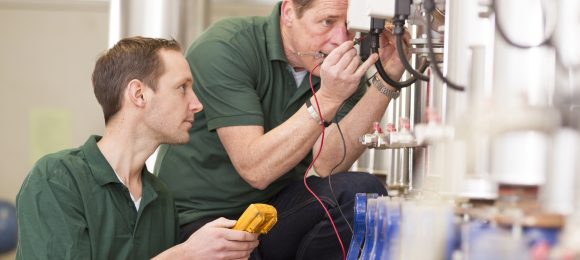
9Nov
Dès la conception, pensez à la maintenance !
Aujourd’hui, alors que la fiabilité des machines automatisées s’est nettement améliorée, le responsable d’exploitation est en droit d’attendre de ses équipements une productivité maximale afin d’optimiser les taux de service. Car tout arrêt non programmé coûte cher, en impactant la production bien sûr, mais aussi les délais de livraison, la chaîne logistique… C’est pourquoi il est important d’intégrer, dès la conception d’une nouvelle machine, les modalités précises de sa maintenance, en travaillant notamment sur l’accessibilité aux différents organes. Cet enjeu majeur pour l’ensemble des composants « sensibles » de l’équipement s’applique bien sûr aux éléments de guidage, comme les axes linéaires ou les glissières télescopiques.
La maintenance : anticiper sur ce qui est probable
Même si les équipements industriels sont de plus en plus fiables, on ne peut totalement écarter le risque d’un aléa imprévisible qui entraînera une panne inédite. À l’impossible, nul n’est tenu ! Mais le principal enjeu de la maintenance, ce n’est pas de parer l’imprévu, mais bien d’anticiper sur les événements probables de la vie d’un équipement. C’est de prévoir ce qui arrivera si l’on n’agit pas à temps : par exemple, la défaillance d’un organe qui a atteint sa durée de vie théorique.
Selon une norme européenne datant de 2001 (NF EN 13306 X 60-319), la maintenance se définit comme : « Ensemble de toutes les actions techniques, administratives et de management durant le cycle de vie d’un bien, destinées à le maintenir ou à le rétablir dans un état dans lequel il peut accomplir la fonction requise. »
Trois différents niveaux de maintenance
Dans une situation idéale, les opérations de maintenance s’effectuent lors d’un arrêt programmé de la machine, sans impact sur la production. Mais en réalité, tout ne se passe pas toujours idéalement…
C’est pourquoi on distingue aujourd’hui trois différents niveaux de maintenance :
- La maintenance préventive organise un planning des différentes opérations d’entretien ou de remplacement des pièces d’usure.
- La maintenance prédictive, ou prévisionnelle, effectue un suivi de la dégradation des composants pour optimiser la date de leur remplacement.
- La maintenance curative agit en dernier lieu, lorsque la panne s’est produite, souvent dans des circonstances exceptionnelles, par définition imprévues et donc non assurées par les deux niveaux précédents.
Faciliter les interventions du personnel de maintenance
Quel que soit le cas de figure, programmé ou non, lorsqu’une opération de maintenance s’impose, il est important de faciliter le bon déroulement des interventions des techniciens concernés.
C’est ce constat qui nous amène à intégrer, très en amont, dès la phase de conception de la machine, un examen approfondi des futures opérations de maintenance. Cela implique de « penser » les différents gestes qui seront pratiqués par le personnel chargé de la maintenance.
Découvrez comment gagner en rapidité dans la maintenance ferroviaire !
Favoriser l’accessibilité, c’est limiter les temps d’intervention
Si l’on arrive à diminuer au maximum la durée de l’opération, l’impact négatif de la maintenance sur la productivité sera également limité en proportion du gain de temps obtenu. Il est donc fondamental de prévoir un accès rapide et aisé à toutes les zones-clés de l’équipement. Ce critère de l’accessibilité devra absolument être pris en compte dès les premières études lorsqu’il faudra, par exemple, démonter un élément très massif ou plus simplement extraire un tiroir.
Dans le domaine ferroviaire, l’accès aux parties inférieures d’un wagon, ou à de lourdes batteries d’accumulateurs, peut être amplement facilité par l’adoption de systèmes amovibles équipés de glissières télescopiques.
De même, le démontage d’un axe linéaire peut s’avérer très difficile si un boulon de fixation se trouve dans un recoin exigu de la machine. Le déplacement de quelques centimètres de l’usinage du trou peut faire gagner de précieuses minutes.
Pour en savoir plus sur les axes linéaires, consultez notre infographie !
Certaines opérations peuvent s’effectuer à chaud, mais d’autres nécessitent l’arrêt
Parmi les nécessaires étapes de cette réflexion globale sur la maintenance, il importe aussi de s’interroger sur un fait : si certaines opérations nécessitent l’arrêt de la machine, d’autres peuvent s’effectuer en phase de fonctionnement. Ainsi, des opérations courantes d’entretien comme le graissage doivent questionner le concepteur non seulement sur l’accès à la zone à graisser, mais aussi sur l’emplacement du graisseur. Très concrètement, si le graisseur est mal placé, son remplissage pourrait souiller de lubrifiant des parties non souhaitées !
Dans les cas où l’arrêt de l’équipement est nécessaire pour remplacer une pièce défectueuse, les interventions peuvent être facilitées si la conception de la machine intègre des sous-ensembles aisément démontables. Cela permettra, encore une fois, d’optimiser les temps de remplacement.
Quel que soit le domaine d’application concerné – machines-outils, robotique, transport – il est particulièrement crucial de se poser très en amont ces différentes problématiques de maintenance. C’est la bonne stratégie pour en diminuer les budgets – en matériel comme en personnel – et pour augmenter à la fois la fiabilité et la rentabilité, donc la performance opérationnelle de son outil industriel.
Crédit photo : Fotolia